摘要:提出了基于成本的長輸管道腐蝕缺陷的檢測及維修模型,將總成本分為檢測和維修2部分,根據(jù)總成本最小原則確定最優(yōu)檢測及維修規(guī)劃。最優(yōu)的檢測及維修,是在保證管道在設(shè)計工作壽命內(nèi)的最大腐蝕深度小于滿足強(qiáng)度要求的最大腐蝕裕量的基礎(chǔ)上,使管道生命周期內(nèi)總的期望費用最小。針對腐蝕缺陷的發(fā)展過程,以最早產(chǎn)生缺陷的尺寸為界限進(jìn)行劃分,對不同腐蝕程度缺陷進(jìn)行分類修復(fù)。通過比較在不同的狀態(tài)點下進(jìn)行檢測修復(fù)所產(chǎn)生的檢測和維修總費用,確定最優(yōu)的檢測及維修規(guī)劃。
關(guān)鍵詞:長輸管道;腐蝕缺陷;檢測;維修;成本
Cost-based Inspection and Repair Planning for Corrosion Defects in Long Distance Pipeline
YU Shu-rong,HE Na,GU Sheng-bin
Abstract:A cost-based inspection and repair model for corrosion defects in 10ng distance pipeline is proposed. The total cost is dived into two parts,one for inspection and another for repair. The optimal inspection and repair planning is determined according to the maximum principle of the total cost. The optimal inspection and repair are to keep the total expected cost to a minimum in pipeline life cycle,ensuring that the maximum corrosion depth of pipeline in design service life is less than the maximum corrosion margin that meets the strength requirement. Taking the size of the earliest generated defect as a limit,the corrosion defects are divided for their development,and the corrosion defects with different corrosion degrees are classified and repaired. The optimal inspection and repair planning is determined by comparing the total cost of inspection and repair at different corrosion states.
Key words:long distance pipeline;corrosion defect;inspection;repair:cost
為防止燃?xì)夤艿朗?,確保管道正常運行,需要對管道進(jìn)行定期檢測,以便及時發(fā)現(xiàn)缺陷進(jìn)行維修。由于管道長期埋在地下,過于頻繁的檢測將增加運行成本,而減少檢測次數(shù),又將降低運行的安全性。如何合理地配置資源,在確保管道安全運行的同時,使管道在壽命期內(nèi)的檢測及維修成本最少?基于此問題提出了基于成本的最優(yōu)檢測及維修規(guī)劃,對管道檢測及維修所產(chǎn)生的費用建立數(shù)學(xué)模型,通過分析計算確定合理的檢測間隔和維修方法。
管道在運行過程中,受許多隨機(jī)因素的影響,目前對于管道檢鋇0及維修規(guī)劃的研究主要集中在應(yīng)用概率數(shù)理統(tǒng)計方法建立數(shù)學(xué)模型,如用馬爾科夫過程、伽馬過程[1]、泊松過程等進(jìn)行模擬,通過模型分析計算管道失效概率和優(yōu)化維修決策。針對不同位置的管道建立符合實際的優(yōu)化檢測和維修規(guī)劃,Bruno Castanier[2]根據(jù)單位時間平均維修成本最小來確定檢測間隔,提出了海底輸油管道的優(yōu)化維修策略。Mitra Fouladirad[3]研究了非穩(wěn)定劣化過程,在運行狀態(tài)突然變化時,從正常狀態(tài)到緊急狀態(tài)的轉(zhuǎn)變維修決策。M.J.Kallen[4]用伽馬過程模擬在不確定狀態(tài)下由于腐蝕引起的壁厚減薄,建立了貝葉斯更新理論模型,模型中納人了對不準(zhǔn)確的檢測結(jié)果的分析。H.Hong[5]研究了考慮新腐蝕缺陷發(fā)展的維修計劃,用馬爾科夫過程模擬了腐蝕缺陷的剩余強(qiáng)度,用泊松過程模擬了新腐蝕缺陷的發(fā)展,基于可靠性極限選擇最優(yōu)檢測和維修規(guī)劃。這種方法考慮了無損檢測工具在檢測缺陷時的不確定性及新缺陷在管道服役期產(chǎn)生的隨機(jī)性,應(yīng)用均勻連續(xù)時間馬爾科夫鏈來模擬剩余負(fù)載率對腐蝕缺陷尺寸的影響,用泊松過程模擬新缺陷的發(fā)展,馬爾科夫狀態(tài)表示管道的操作壓力與腐蝕管道剩余強(qiáng)度壓力的比值,通過解Kolmogorov微分方程獲得轉(zhuǎn)移概率矩陣。
1 檢測及維修模型
針對腐蝕缺陷的產(chǎn)生過程進(jìn)行分析,筆者提出了一種基于成本的腐蝕缺陷的檢測及維修規(guī)劃,認(rèn)為最早產(chǎn)生的缺陷是每次檢測中缺陷尺寸最大的,缺陷產(chǎn)生的過程是隨機(jī)過程,對隨機(jī)產(chǎn)生的缺陷,假設(shè)同一區(qū)域的所有缺陷按照相同的過程進(jìn)行發(fā)展,以該區(qū)域最早產(chǎn)生的缺陷的尺寸為界限,進(jìn)行維修區(qū)間劃分,確定相應(yīng)狀態(tài)的修復(fù)措施。
1.1 最大腐蝕裕量的計算
最優(yōu)的檢測及維修,是在保證結(jié)構(gòu)在設(shè)計工作壽命內(nèi)的可靠度指標(biāo)大于最低可靠度指標(biāo)的基礎(chǔ)上進(jìn)行的優(yōu)化[6]。為預(yù)防失效的發(fā)生,管壁的厚度減薄量應(yīng)小于最大腐蝕裕量。由文獻(xiàn)[7]知,對于管道的腐蝕,其腐蝕狀態(tài)函數(shù)由下式進(jìn)行定義:

式中g(t)——腐蝕狀態(tài)函數(shù),MPa
σ——材料的屈服極限,MPa
v——腐蝕速率,mm/a
t——腐蝕時間,a
δ——管壁厚度,mm
p——操作壓力,MPa
d——管道外徑,mm
式(1)為強(qiáng)度隨壁厚減薄而降低的應(yīng)力強(qiáng)度模型,公式中
表示管道實際的剩余強(qiáng)度,
表示管道在操作壓力下必須達(dá)到的強(qiáng)度,vt表示管壁在t內(nèi)的腐蝕減薄量,當(dāng)g(t)=0求得:
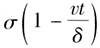


式中m——最大壁厚減薄量,mm
在計算過程中如果考慮設(shè)計、焊接、溫度等因素的影響,m的取值見式(3)[8]:
m=δ-δmin (3)
式中δmin——最小安全壁厚,mm

式中F——強(qiáng)度設(shè)計系數(shù)
φ——焊縫系數(shù)
τ——溫度折減系數(shù)
各系數(shù)具體取值參見文獻(xiàn)[8]。
1.2 基于成本的檢測及維修優(yōu)化模型
① 模型建立的幾點假設(shè)
腐蝕缺陷產(chǎn)生的前提條件是防腐層破壞,進(jìn)而導(dǎo)致管壁減薄。管道所處的地段不同,防腐層施工質(zhì)量不同,腐蝕缺陷產(chǎn)生的時間也不同。為了方便模型的描述,做以下假設(shè):
a. 不考慮防腐層的老化,同一管段1km的管道上產(chǎn)生1個腐蝕缺陷的平均時間為t。。
b. 缺陷腐蝕為勻速腐蝕,腐蝕速率為穢。
c. 檢測為完備性檢測,即每次都檢測出了所有腐蝕缺陷。
d. 缺陷修復(fù)后達(dá)到修舊如新的狀態(tài)
② 檢測及維修相關(guān)說明
模型中用Ci(單位為元/(km·次))表示單位管道每次的檢測費用。對于管道的修復(fù),由于維修技術(shù)的限制,不同的管道公司采用的修復(fù)技術(shù)不同,且對不同腐蝕程度的缺陷采取的修復(fù)方法也不I司,本文將缺陷的腐蝕程度分為輕、中、重3種,針對不同程度的腐蝕缺陷采用不同的修復(fù)方法。
沿壁厚方向?qū)⑷毕莸陌l(fā)展劃分成4個階段,見圖1。在模型的實際應(yīng)用過程中,可根據(jù)實際供選擇的維修方式進(jìn)行腐蝕階段和維修種類的劃分。用△δ表示缺陷的腐蝕深度,在圖1中的點4處,腐蝕深度達(dá)到最大,即δ1+δ2+δ3=m。
第1階段(0—1段):防腐層破壞階段;
第2階段(1—2段):缺陷需要輕度維修階段,△δ≤δ1;
第3階段(2—3段):缺陷需要中度維修階段,δ1<△δ≤δ1+δ2;
第4階段(3—段):缺陷需要重度維修階段,δ1+δ2<△δ≤δ1+δ2+δ3
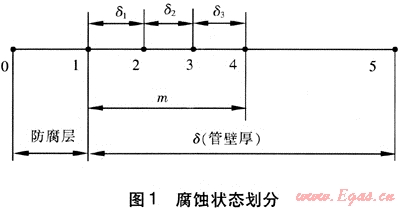
④ 不同狀態(tài)下發(fā)生的檢測費用
在運行過程中,因為缺陷的產(chǎn)生是隨機(jī)過程,所以很難把握圖中點l的狀態(tài),即防腐層一旦失效便進(jìn)行檢測修復(fù),所以從點2狀態(tài)開始分析,各狀態(tài)的分析結(jié)果見表1,表中T(單位為a)為管道的使用壽命,l(單位為km)為所計算管段的長度。由于檢測間隔和檢測次數(shù)為整數(shù),定義函數(shù)inte[f(x)]為f(x)值的整數(shù)部分,若計算所得檢測次數(shù)為整數(shù),按實際運行壽命中檢測發(fā)生的次數(shù),最后一次檢測(即管道運行時間已到使用壽命時進(jìn)行的檢測)不考慮進(jìn)檢測維修規(guī)劃中,則實際發(fā)生的檢測次數(shù)應(yīng)為計算值減去1,在以下的計算中檢測間隔和檢測次數(shù)都按照這個方法進(jìn)行計算。
⑤ 不同狀態(tài)下發(fā)生的維修費用
在已有缺陷不斷腐蝕的情況下,新缺陷也在隨機(jī)產(chǎn)生,所以在每個狀態(tài)點檢測維修時,都包括前面狀態(tài)下的腐蝕缺陷,如在點4狀態(tài)時缺陷的維修方式有3種:輕度維修、中度維修和重度維修。假設(shè)單位缺陷的輕度、中度、重度維修成本分別為Cr1(單位為元/個)、Cr2(單位為元/個)、Cr3(單位為元/個),則在每個狀態(tài)下修復(fù)所產(chǎn)生的維修費用見表2。
在表2中,因為檢測間隔以a為單位,所以將檢測間隔取整后,檢測間隔小于實際計算值,最大缺陷在檢測時沒有達(dá)到狀態(tài)點劃分的尺寸值,故對于點3處進(jìn)行維修時,中度維修的最大缺陷為δx,δx由下式確定:

同理,點4處維修時的最大缺陷為δy:


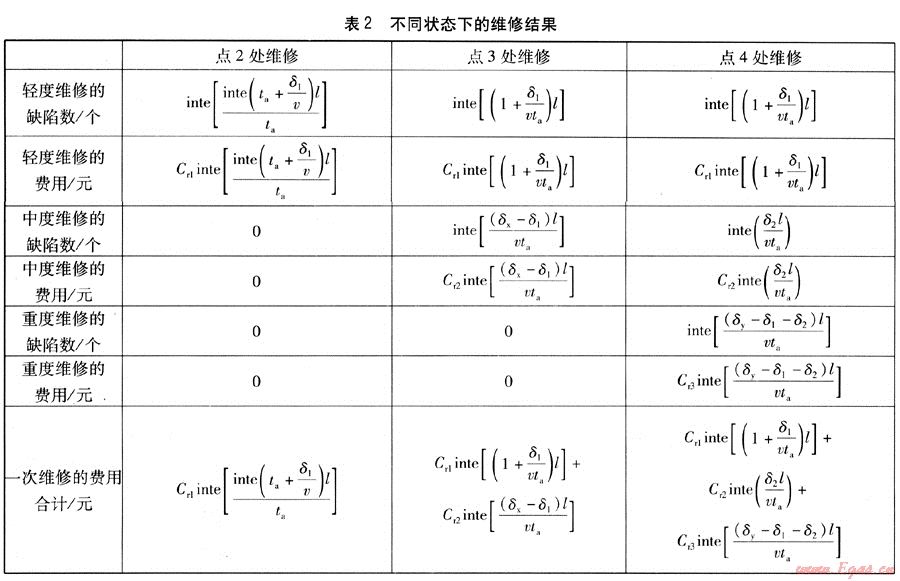
?、?總的費用分析
管道在運行過程中,不同的區(qū)域腐蝕速率和單位腐蝕缺陷產(chǎn)生的時間t。不同,根據(jù)不同的腐蝕狀態(tài)對管道進(jìn)行區(qū)域劃分,將腐蝕發(fā)展?fàn)顟B(tài)相同的區(qū)域歸為一類,假設(shè)有n個區(qū)域??傎M用包括檢測費用和維修費用,由表1與表2可得管道設(shè)計壽命內(nèi)點2、3、4狀態(tài)檢測、維修的總費用,分別見式(7)、(8)、(9)。
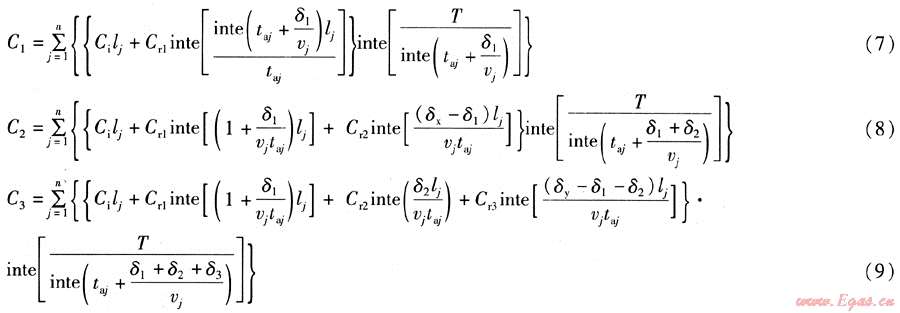
式中C1、C2、C3——點2、3、4狀態(tài)下檢測和維修的總費用,元
lj——第j個區(qū)域中管道的長度,km
taj——第j個區(qū)域管道單位缺陷產(chǎn)生的時間,a
vj——第j個區(qū)域管道的腐蝕速率,mm/a
取C1、C2、C3中最小值,則相應(yīng)的檢測維修規(guī)劃即為最優(yōu)檢i貝4及維修規(guī)劃。
2 算例
某管道[9~11]采用Ø273×7的X52直縫鋼管,最大工作壓力為5.8MPa,設(shè)計壽命為20a,假設(shè)其中長102.7km的管段從開始投產(chǎn)到檢測時,中間沒有進(jìn)行過維修,同時此管段的腐蝕狀況相同,根據(jù)檢測時間、檢測出的缺陷數(shù)以及缺陷的最大尺寸,算得單位缺陷產(chǎn)生的時間ta=0.933a,腐蝕速率v=0.6mm/a,缺陷腐蝕程度范圍和單位缺陷的維修費用見表3,檢測費用Ci=8000元/(km·次)。將數(shù)據(jù)代入上述公式計算,結(jié)果見表4。
表3 維修范圍及費用
項目
|
輕度維修
|
中度維修
|
重度維修
|
缺陷范圍
|
△δ/mm≤1.5
|
1.5<△δ/mm≤3.0
|
3.0<△δ/mm≤3.9
|
單位缺陷修復(fù)的費用/(元·個-1)
|
500
|
800
|
1500
|
表4 檢測及維修相關(guān)計算結(jié)果
項 目
|
點2狀態(tài)
|
點3狀態(tài)
|
點4狀態(tài)
|
檢測間隔/a
|
3
|
5
|
7
|
檢測次數(shù)/次
|
6
|
3
|
2
|
輕度腐蝕缺陷數(shù)/個
|
330
|
377
|
377
|
中度腐蝕缺陷數(shù)/個
|
0
|
172
|
275
|
嚴(yán)重腐蝕缺陷數(shù)/個
|
0
|
0
|
117
|
總檢測費用/元
|
4929600
|
2464800
|
1643200
|
總維修費用/元
|
990000
|
978300
|
1168000
|
總費用/元
|
5919600
|
3443100
|
2811200
|
從表4結(jié)果可見:對于所選管段,檢測間隔為7a時檢測維修成本最低,故對此管段,最優(yōu)的檢測及維修規(guī)劃為在管道使用壽命期內(nèi)每7a檢測1次。
3 結(jié)論
① 提出了基于成本的管道檢測及維修規(guī)劃的計算方法和思路,并以實例進(jìn)行了計算分析。
② 檢測方法和維修方法的選擇影響檢測維修規(guī)劃的制定,不同管段因腐蝕情況不同,其檢測維修規(guī)劃也不同。在實際運行中,應(yīng)根據(jù)不同的腐蝕機(jī)理、不同的腐蝕影響因素對模型進(jìn)行區(qū)分應(yīng)用。
參考文獻(xiàn):
[1] VAN NOORTWIJK J M.A survey of the application of gamma processes in maintenance[J].Reliability Engineering and System Safety,2009,(94):2-21.
[2] CASTANIER B,RAUSAND M. Maintenance optimization for subsea oil pipelines[J].Pressure Vessels and Pipeline,2006,(83):236-243.
[3] FOULADIRAD M,CRALL A,DIEULLE L. On the use of on-line detection for maintenance of gradually deteriorating systems[J].Reliability Engineering and System Safety,2008,(93):1814-1820.
[4] KALLEN M J,VAN NOORTWIJK J M. Optimal maintenance decisions under imperfect inspection[J].Reliability Engineering and System Safety,2005,(90):177-185.
[5] HONG H. Inspection and maintenance planning of pipeline under external corrosion considering generation of new defects[J].Structural Safety,1999,(21):203-222.
[6] 李典慶,張圣坤,唐文勇.基于風(fēng)險的船體結(jié)構(gòu)腐蝕優(yōu)化檢測及維修規(guī)劃[J].上海交通大學(xué)學(xué)報,2004,(38):1875-1879.
[7] API 581,Risk-based inspection-base resource document[S].
[8] SY/T 0087.1—2006,鋼制管道及儲罐腐蝕評價標(biāo)準(zhǔn)埋地鋼制管道外腐蝕直接評價[s].
[9] 陸新東,盧宇光,陳祥嶺,等.漏磁腐蝕檢測技術(shù)在二連油田阿賽輸油管道上的應(yīng)用[J].內(nèi)蒙古石油化工,1998,(24卷增刊):32-34.
[10] 羅衛(wèi)國,趙新偉,白真權(quán),等.阿賽輸油管道腐蝕狀況調(diào)查及分析[J].焊管,2004,(27):14-17.
[11] 王獻(xiàn)防,白真權(quán),韓曉毅.阿一賽輸油管道腐蝕現(xiàn)狀分析[J].全面腐蝕控制,2003,(17):13-16.
(本文作者:俞樹榮1 何娜1 顧生斌2 1.蘭州理工大學(xué)石油化工學(xué)院 甘肅蘭州 730050;2.西氣東輸管道公司 甘肅管理處 甘肅武威 733000)
贊 賞 分享
您可以選擇一種方式贊助本站
支付寶轉(zhuǎn)賬贊助
微信轉(zhuǎn)賬贊助

- 注解:本資料由會員及群友提供僅供閱讀交流學(xué)習(xí),不得用于商業(yè)用途!