摘要:因液化石油(LPG)回收系統(tǒng)的天然氣壓縮機潤滑系統(tǒng)的生產工藝流程設計存在不足,致使未凝氣帶液進入壓縮機,造成潤滑油污染,導致軸承和潤滑油泵潤滑不良,磨損加劇,使用壽命降低。為此,通過壓縮機軸承和滑油泵失效損壞分析,對機組系統(tǒng)的油氣路進行了改造優(yōu)化:拆除滌氣罐內除沫網,改裝19根高效過濾精度在O.05μm的頗爾纖維濾芯;啟用10μm不銹鋼磁性過濾器;將回油管線引入常溫分離器,利用兩端壓力差排液,同時利用常溫分離器的功能進行油氣水分離。由此改善了軸承和滑油泵的潤滑狀況;對操作參數進行了調整,提高了壓縮機運行穩(wěn)定性和生產時效性,每年節(jié)省維修費用約t10萬元(還沒有計入停機損失的費用),取得了較好的經濟效益。
關鍵詞:LPG;雙螺桿壓縮機;潤滑油泵;出口凝聚過濾器;進口滌氣罐;潤滑系統(tǒng);優(yōu)化
文昌13-1/2油田FPSO(浮式生產裝置)的LPG回收項目是中國海洋石油(中國)有限公司湛江分公司從節(jié)約能源、保護環(huán)境的理念出發(fā),利用FPSO回收原油伴生氣而啟動的改造項目,該項目的實施,能有效提高對能源的回收率和利用率,并減少二氧化碳等溫室氣體的排放量,同時能取得更好的社會經濟效益。
該裝置的主要回收壓縮模塊配置了兩臺由美國SULLAIR公司生產的PCV40L-50-IOM型噴油式雙螺桿壓縮機,設計排量為3398.3m3/d,最大功率為511.4kW,壓縮機潤滑油使用CPI CP-1516-150冷凍機油1000L(SULL AIR公司,Compressor Operation Manual),主要用于把天然氣從20~50kPa升壓至1200kPa,以滿足LPG回收系統(tǒng)生產工藝的壓力需求。該壓縮機機組在2006年10月投產運行,因為原流程設計不合理,在運行過程中出現(xiàn)了壓縮機和潤滑油泵故障,為此對故障原因進行了分析,并提出了相應的改造措施。
1 壓縮機軸承和潤滑油泵失效損壞分析
圖1是LPG壓縮機生產系統(tǒng)和潤滑油流程示意圖。組分為C3+、C4+的天然氣從一級分離器分離后至進口滌氣罐V-3610,清除游離態(tài)的液滴,進入壓縮機K-3620A/B,壓縮機將原料氣從20kPa壓縮至1206.6kPa,最終在出口凝聚過濾器內部進行油氣分離[1]。原進口滌氣罐內鋼絲除沫網無法徹底分離液體,導致含有輕質油組分和水分進入壓縮機潤滑油系統(tǒng)壓縮,使?jié)櫥褪艿轿廴救榛捅幌♂?,潤滑物理性能降低。機組運行時要把潤滑油內的水分和輕組分分離,需提高出口溫度來達到目的。經驗數據表明:潤滑油溫度每提高10℃,黏度就會降低50%[2]。因此,壓縮機在高溫、潤滑效果欠佳的情況下運行,會導致自帶滑油泵驅動銷斷裂頻繁和內部齒輪磨損過快而損壞。更嚴重的是壓縮機螺桿主副軸承磨損后產生振動上升,軸承內滾道慢慢剝落,最終造成振動高而非正常關停,由此帶來的經濟損失約為30萬元/d。為此,必須對機組系統(tǒng)流程進行分析和評估,對壓縮機的油氣路流程進行部分改造,以優(yōu)化、改善壓縮機運行環(huán)境。
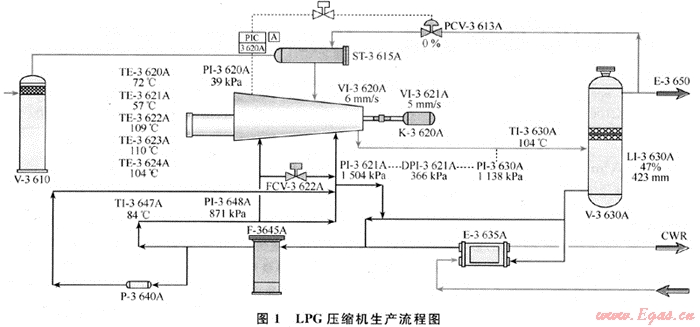
2 優(yōu)化方案
2.1 進口滌氣罐改造
通過項目調研評估和可行性分析,決定拆除滌氣罐內除沫網,改裝19根高效過濾精度在0.05μm的頗爾纖維濾芯,方案經過數次討論優(yōu)化,確定全部預制好到現(xiàn)場安裝,具體設計方案如圖2~4。
1) 加工3塊平管板(每塊重約20kg),如圖2所示。

2) 用直流手電鉆在滌氣罐下裙邊上鉆8個Ø10mm的孔,將2條槽鋼架在裙邊上面硬板用4-M8螺栓固定,用2條角鋼附于裙邊下面與槽鋼邊成一體加固,安裝管板井字吊架,然后安裝1號大的管板,再裝2號(中間)管板,最后進行濾芯安裝,人從罐體上部下到罐體下部進行第三塊管板的安裝如圖3所示。

3) 在管板四周和管板之間的連接部分采用圓形橡膠條和膠墊密封,如圖4所示。

2.2 油路改造
2.2.1潤滑油過濾器改造
原配套0.5μm纖維濾芯精度過小,壓縮機因潤滑油壓差過大經常停機,重新訂購10μm不銹鋼磁性過濾器,在過濾雜質的同時可以有效將金屬雜質吸附到濾芯上,減少壓縮機內部運動部件因雜質而造成的二次損傷。
2.2.2出口凝聚過濾器回油管線改造
在運行過程中取樣檢查時發(fā)現(xiàn)出口凝聚過濾器原設計的回油管線有大量的液體返回到壓縮機進口,取樣分析內含輕質油、水和潤滑油,其中輕質油占80%,水占15%,滑油占5%。關閉回油管線10min后取樣回收液量1200mL,按此計算一個月累計有510L,如此多液體返回系統(tǒng)循環(huán),增加了二次污染。針對此情況,果斷地將回油管線進行流程改造,將管線引入常溫分離器,利用兩端壓力差排液,同時利用常溫分離器的功能進行油氣水分離。改造如圖5所示。
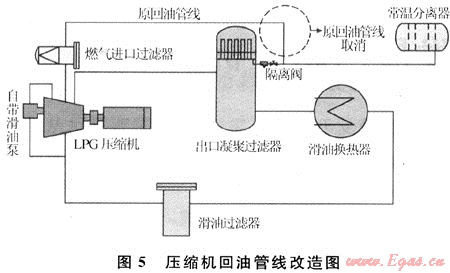
3 優(yōu)化效果
3.1 優(yōu)化效果
1)加裝了19根0.05μm高效分離器濾芯后,進口滌氣罐排液能力從原來的15L/h增加到45L/h,
2) 出口凝聚過濾器取油樣化驗顯示輕質油含量明顯減少,含水量0.01%,不存在乳化現(xiàn)象。
3) 未改造前壓縮機振動曲線振幅波動較大,改造后,振動曲線乎直而且平穩(wěn),反映出壓縮機在得到良好潤滑后運行平穩(wěn)。
4) 壓縮機因自帶泵故障造成非正常停機次數由原來每月平均3次,降低為兩個月1次。
5) 壓縮機改造前平均壽命3個月,改造后連續(xù)運轉5個月沒有出現(xiàn)故障。
6) 節(jié)省壓縮機大修維修費用約25萬元/次,減少停機損失約30萬元/d。
7) 對比改造前、后的關鍵運行參數(如表1所示)可以看出改造后壓縮機運轉各項參數較為平穩(wěn),而且出口溫度和潤滑油溫度明顯降低5℃左右。
表1 壓縮機系統(tǒng)改造前、后運行參數對照表
描述
|
參數
|
改造前(2008年1~10月)
|
改造后(2008年11月~2009年3月)
|
||||||||||||
1月
|
2月
|
3月
|
4月
|
5月
|
7月
|
8月
|
9月
|
10月
|
11月
|
12月
|
1月
|
2月
|
3月
|
||
出口溫度(℃)
|
<110
|
104
|
103
|
106
|
106
|
107
|
107
|
107
|
107
|
108
|
103
|
103
|
102
|
102
|
102
|
油溫(℃)
|
<85
|
85
|
83
|
86
|
85
|
86
|
89
|
88
|
88
|
87
|
80
|
82
|
81
|
82
|
83
|
壓縮機振動(mm/s)
|
<7.62
|
7.2
|
5.4
|
6
|
6
|
6
|
4
|
4
|
4
|
6.4
|
4
|
5
|
5
|
5.5
|
5.5
|
馬達振動(mm/s)
|
<20
|
4.8
|
4.4
|
5
|
5
|
4.5
|
3.6
|
4
|
4
|
4.2
|
4
|
4
|
4
|
4
|
4
|
注:表中數據為月平均值。
3.2 優(yōu)化效益
LPG壓縮機系統(tǒng)油氣路改造費用為39.5萬元,項目改造完后,因為修理工作量減少,經粗略計算每年節(jié)省維修費用約110萬元(還沒有計入停機損失的費用),取得了較好的經濟效益。
4 結論
1) 通過以上對LPG壓縮機油、氣系統(tǒng)的改造,提高了整個生產系統(tǒng)的穩(wěn)定性和時效性,為相關生產單位提供了良好借鑒作用。
2) 建議在設計生產系統(tǒng)的初期,必須考慮工藝和下游設施設備的配套性,防止造成不利影響。
參考文獻
[1] 張保山,王治國.文昌13-1/2油田LPG回收培訓手冊[G].海南文昌:文昌13-1/2油田,2001.
[2] 孫占禮.天然氣加工機器與設備[M].天津:天津科學技術出版社,1994.
(本文作者:陳汝澤 周天育 葉冠群 黃敢 蘇華軍 中國海洋石油(中國)有限公司文昌13-1/2油田作業(yè)公司)
贊 賞 分享
您可以選擇一種方式贊助本站
支付寶轉賬贊助
微信轉賬贊助

- 注解:本資料由會員及群友提供僅供閱讀交流學習,不得用于商業(yè)用途!